Если я прошла курс где мой сертификат |
Экозащитные технологические мероприятия на нефтегазовых объектах
Изоляция труб и испытания магистральных трубопроводов
Защита МТ от подземной коррозии осуществляется комплексно: защитными (изоляционными) покрытиями и средствами электрохимической защиты.
Изоляционные покрытия должны удовлетворять следующим требованиям:
- быть сплошными и обладать высокими диэлектрическими свойствами;
- обладать хорошей адгезией и водонепроницаемостью;
- обладать термостойкостью, биостойкостью и механической прочностью.
В зависимости от используемых материалов различают покрытия на основе битумных мастик, полимерных липких лент, эпоксидных полимеров, каменноугольных пеков, стекло-эмалевых покрытий и др. Наибольшее распространение получили покрытия на основе битумных мастик.
В зависимости от условий прокладки и эксплуатации применяют покрытия: усиленные и нормальные.
Усиленные покрытия применяют на трубах со сжиженными углеводородами, трубах диаметром 1020 мм и более, в засоленных и болотистых почвах, на подводных и других переходах, при температуре продукта выше . Это покрытие включает в себя грунтовку, слой битумно-резиновой мастики толщиной 6 мм, слой стеклохолста и защитную обертку. Усиленное покрытие также может выполняться из двух слоев полимерной ленты.
В большинстве остальных случаев используется нормальное покрытие, которое включает в себя битумную грунтовку, слой битумно-резиновой мастики до 4 мм, слой стеклохолста и защитную обертку.
Изолируемые трубы перед нанесением грунтовочного слоя очищаются от ржавчины, масел и пыли.
Битумно-полимерные грунтовки изготавливают в заводских условиях. Битумно-резиновые грунтовки и мастики приготовляются на месте растворением битума в бензине. Слой грунтовки заполняет микронеровности на поверхности металла и служит для обеспечения лучшей адгезии между поверхностью металла и основным изоляционным слоем.
Битумные мастики приготавливают в заводских условиях; в трассовых условиях - их разогревают в котлах до .
В состав мастик входит битум до 90%, резиновая крошка - до 12%, пластификатор - до 7% и наполнитель (доломит, известняк, тальк).
Нанесение покрытий производится изоляционными машинами. На изолирующей обечайке устанавливается необходимый зазор между обечайкой и трубой.
Армирование битумного покрытия стеклохолстом и рулонными материалами осуществляется спирально без морщин и складок с нахлестом не менее 30 мм. Ширина рулонного материала не более 50 см.
Рулонные материалы наносят одновременно с изоляцией по слою горячей мастики путем намотки по спирали той же изоляционной машиной.
Клеевые грунтовки, изоляционные ленты и обертки наносятся на трубу одновременно механизированным способом. Для обеспечения плотного прилегания лент и оберток необходимо постоянное натяжение материала с определенным усилием.
Тип полимерного покрытия выбирается в зависимости от температуры транспортируемого продукта. Порошковые полиэтиленовые покрытия применяют при , эпоксидные - при
, полиэтиленовые липкие ленты - при
. поли-винилхлоридные липкие ленты - при
.
Усиленные полимерные покрытия имеют толщину до 3 мм. Они очень технологичны, изготавливаются в основном в заводских условиях.
Крановые узлы, задвижки, катодные выводы изолируются битумными мастиками или полимерными липкими лентами.
Трубные плети укладывают в траншею в зависимости от местных условий и диаметра труб одним из нескольких способов.
Для обеспечения сохранности изоляционного покрытия при укладке плетей в траншею нельзя допускать их соприкосновения со стенками траншеи. Дно траншеи должно быть выровнено мягкой подсыпкой. Обетонированные трубы и трубы с футеровкой дополнительной защиты от повреждений не требуют.
Гидравлические испытания трубопроводов
Перед сдачей в эксплуатацию трубопровод должен быть очищен от посторонних предметов, грязи и пыли. Очистка производится после выполнения всех видов работ: при подземной схеме укладки трубопровод должен быть уложен в траншею и засыпан грунтом, при наземной - уложен и обвалован грунтом, при надземной - уложен на опоры и закреплен.
Основным способом очистки полости трубы является пропуск по ней специальных очистных устройств с помощью воздуха или газа, а также с помощью воды.
Для продувки трубопровода требуется высокое давление воздуха, чтобы обеспечить поршню движение со скоростью до 60 км/ч. После заполнения ресивера (накопителя воздуха) воздух подают в продуваемый участок, куда уже помещен поршень. Под давлением воздуха поршень очищает трубопровод и вылетает в специальный патрубок.
При промывке полости труб водой решаются одновременно две задачи: трубопровод очищается от грязи и заполняется водой для последующего гидравлического испытания. Длина участков, промываемых за один проход поршня, может достигать 50 км.
Расчетная прочность трубопровода - это характеристика, учитывающая все предполагаемые факторы, которые могут привести к его разрушению.
В процессе строительства трубопровода за всеми технологическими операциями осуществляется строгий контроль, однако высокая эксплуатационная надежность может быть обеспечена только после проведения испытания на прочность всей линейной части и различных узлов трубопровода.
На заводе трубы испытывают кратковременным приложением давления, которое вызывает кольцевые напряжения, близкие к пределу текучести. Однако проверить соответствие расчетной прочности трубопровода действительной прочности в условиях эксплуатации трубопровода можно только испытанием внутренним давлением, при котором выявляются все необнаруженные дефекты.
Испытания проводят водой. В зависимости от категории участков принимают от одного до трех испытаний с определенными максимальными величинами давлений. При проверке на прочность испытания проводятся в течение 24 ч, на герметичность - 12 ч. Испытательное напряжение не должно вызывать в металле напряжений более 0,9 предела текучести.
Первый этап испытаний осуществляют на площадке до нанесения изоляции для участков категорий В и I при давлении . Второй этап испытаний проводится после укладки, но до засыпки трубопровода. При этом отдельные испытываемые участки ограничиваются заглушками или линейной арматурой. На третьем этапе трубопровод испытывается одновременно с прилегающими участками.
Испытательное давление в наиболее высокой точке трассы принимается не менее для участков третьей и четвертой категорий;
для участков первой и второй категорий;
для трубопроводов категории В. При испытаниях устанавливается охранная зона по 100 м в обе стороны от трубопровода.
Перед вводом в эксплуатацию трубопроводов, которые были выведены из эксплуатации на срок более одного года, проводятся гидравлические переиспытания. Протяженность испытуемых участков не должна быть больше 40 км.
В процессе выдержки трубопроводов под давлением может изменяться температура воды и стенок труб, вследствие чего будет изменяться давление в трубе. Изменение испытательного давления компенсируется подкачкой или сбросом воды. При резком падении давления и обнаружении выхода воды испытания прерываются.
Результаты гидравлических испытаний на прочность и герметичность признаются удовлетворительными, если не произошло разрывов, падения давления, а в основном металле, сварных швах, арматуре не обнаружено течи и запотеваний. Выявленные при испытаниях дефекты должны быть устранены в порядке, предусмотренном нормативными документами.
Виды коррозии и электрохимическая защита трубопроводов
При рассмотрении многих технических вопросов, таких, например, как истечение нефтепродуктов из резервуаров различного назначения, распыление топлива через форсунки котельных агрегатов и двигателей внутреннего сгорания, утечки нефти через свищи и трещины в стенках трубопроводов, приходится сталкиваться с истечением жидкости через отверстия.
Трубопроводы, резервуары и оборудование в процессе эксплуатации подвергаются процессу коррозии (лат. corrosio - разъедание). Коррозия - это процесс самопроизвольного окисления металла под воздействием окружающей среды, приводящий к его разрушению. Таким образом, конструкцию нужно защищать от ОС, чтобы эта конструкция защищала ту же ОС.
Коррозия труб происходит как снаружи под действием почвенного электролита, так и изнутри вследствие примесей влаги, солей и сероводорода, содержащихся в углеводородном сырье. Коррозия приводит к преждевременному износу агрегатов, трубопроводов, резервуаров.
В зависимости от механизма реакций, протекающих на поверхности металла, коррозия бывает химической и электрохимической.
Химическая коррозия - это процесс разрушения металла при его взаимодействии с газами или жидкостями по законам химических реакций, не сопровождающийся возникновением электрического тока. При этом продукты коррозии образуются на всем участке контакта металла с агрессивной средой. Кинетика этих реакций выглядит следующим образом:
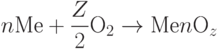
где - число атомов металла в реакции:
- валентность металла.
Электрохимическая коррозия подразделяется на коррозию в электролитах, почвенную, атмосферную и контактную. Во всех случаях окисление металлов происходит за счет возникновения электрического тока, анодные и катодные процессы протекают на различных участках поверхности, а продукты коррозии образуются на анодных участках.
При электрохимической коррозии одновременно протекают два процесса - окислительный (анодный), вызывающий растворение металла на одном участке, и восстановительный (катодный), связанный с выделением катиона из раствора и восстановлением окислителя на другом. В результате возникают микрогальванические элементы, и появляется электрический ток. обусловленный электронной проводимостью металла и ионной проводимостью раствора электролита. Анодные и катодные процессы локализуются на тех участках, где их протекание облегчено.
Причины, вызывающие электрохимическую неоднородность поверхности, многочисленны: макро- и микронеоднородность металла, фазовая и структурная неоднородность сплавов, неоднородность деформаций и напряжений. Неоднородность приводит к образованию микроэлементов (микропар) в местах соприкосновения с грунтом.
Для стальных трубопроводов скорость разрушения зависит от типа грунта, содержания влаги и воздуха в грунте, температуры и удельного сопротивления грунта, наличия бактерий, которые активизируют коррозионные процессы за счет образования сульфатных солей.
Изоляционные покрытия не гарантируют необходимой защиты подземных трубопроводов от коррозии. Практика показывает, что даже тщательно выполненное изоляционное покрытие в процессе эксплуатации стареет: теряет адгезионные свойства и водоустойчивость. Случаются повреждения изоляции при засыпке трубопроводов, при воздействии корней растений. По названным причинам защита трубопроводов от подземной коррозии осуществляется комплексно: защитными покрытиями и средствами электрохимической защиты (ЭХЗ).
При контакте металла трубопровода с почвенными электролитами происходит его окисление, сопровождающееся протеканием электрического тока. На различных участках поверхности трубы возникают катодные и анодные участки. При этом на анодных участках происходит процесс коррозионного разрушения, который начинается с поверхности трубы и затем распространяется вглубь металла.
На интенсивность протекания процессов коррозии оказывают влияние различные факторы: неоднородность состава сталей; различная влажность грунтов и различная минерализация грунтовых вод.
При активных способах защиты трубопроводов от наружной коррозии создается такая электрическая цепь, в которой металл трубопровода является катодом, а дополнительно размещенный в грунте металл - анодом.
При катодной защите положительный полюс источника постоянного тока (анод) подключается к специальному анодному заземлителю, а отрицательный (катод) - к защищаемому трубопроводу ( рис. 8.5).
Принцип действия катодной защиты аналогичен процессу протекания электролиза. Под воздействием электрического поля металл анодного заземлителя теряет электроны, а его ионы переходят в раствор почвенного электролита. Таким образом, разрушению подвергается анодный заземлитель.
Расстояние между заземлителем и трубопроводом может назначаться от 100 до 1 ООО м. Это расстояние определяет срок службы заземлителя (10-15 лет) и необходимое количество станций катодной защиты (СКЗ). Например, при защите трубопровода диаметром 820 мм и удалении заземлителя от трубопровода на 350 м зона влияния одной СКЗ составляет примерно 15 км. Кабель может прокладываться в траншее или по столбам воздушной линии.
Принцип действия протекторной защиты аналогичен принципу действия гальванической пары: рядом с трубопроводом размещают протектор — более активный металл (магний, цинк или алюминий), который соединяют с трубопроводом изолированным проводником. При этом возникает разность потенциалов, под действием которой по кабелю происходит направленное движение электронов от протектора-анода к трубопроводу-катоду. В данном случае разрушению также подвергается протектор, а не трубопровод.
Сила возникающего тока контролируется с помощью специальной контрольно-измерительной колонки. Кабель укладывается в траншею на глубину 0,8 м. Протектор опускается в скважину, которая бурится со дна траншеи. Обычно протекторная защита применяется при прокладке трубопроводов в труднодоступных районах, удаленных от источников электроэнергии.
Электродренажная защита предназначена для защиты трубопроводов от разрушения блуждающими токами. Источником блуждающих токов является электротранспорт, работающий по схеме "провод-двигатель-рельс".
Если поблизости от железной дороги находится трубопровод с нарушенной изоляцией, то стекающий на землю ток пойдет по трубопроводу. Труба - это шунтирующий элемент, снижающий электрическое сопротивление. В месте выхода тока трубопровод может за очень короткое время разрушиться. Сооружения электродренажной защиты отводят блуждающие токи от трубопровода на специальное заземление или возвращают блуждающие токи на их источник. Сила тока в цепи "трубопровод-рельс" регулируется реостатом.
Основной принцип этой защиты состоит в устранении анодных зон путем отвода (дренажа) блуждающих токов в рельсовую часть цепи электротяги ( рис. 8.6), имеющей отрицательный или знакопеременный потенциал. Принципиальная схема электрического дренажа, обеспечивающая прохождение блуждающих токов только в одном направлении из трубопровода в рельс, приводится на рис. 8.6, б.
Работы по сооружению электрохимической защиты осуществляются в две стадии. На первой стадии выполняются работы: разметка трасс ЛЭП и кабелей: доставка оборудования и монтажных узлов; укладка кабелей в траншеях; сооружение заземлений и укладка протекторов; монтаж катодных электрических выводов от трубопроводов, а также контактных соединений анодных и протекторных выводов. Эти работы ведутся одновременно с основными строительными работами по технологической части трубопровода.
На второй стадии устанавливается оборудование, шкафы дренажной защиты, подключаются кабели, и осуществляется пуск и опробование оборудования.
Санитарно-защитные зоны предприятий
Предприятия с технологическими процессами, являющимися источниками негативного воздействия на среду обитания и здоровье человека, должны отделяться от жилой застройки санитарно-защитными зонами (СЗЗ). Эти зоны устанавливаются для объектов, создающих за пределами промплощадки уровни загрязнения выше ПДК или ПДУ.
Ширина СЗЗ устанавливается с учетом результатов расчетов ожидаемого загрязнения атмосферного воздуха и уровней физических воздействий по каждому из факторов, а для действующих предприятий - натурных исследований.
Для магистральных трубопроводов, компрессорных станций создаются санитарные разрывы (полосы отчуждения) с учетом диаметра трубопроводов.
В границах СЗЗ допускается размещать сельхозугодья для выращивания технических культур, объекты торговли, гаражи, поликлиники, учебные заведения, прачечные. ЛЭП, скважины техводоснабжения.
В целях защиты населения от воздействия электрического поля, создаваемого воздушными линиями (ВЛ) электропередачи с напряженностью более 1 кВ/м, устанавливаются санитарные разрывы. Ширина санитарных разрывов для ВЛ напряжением 330 кВ - 40 м, для ВЛ напряжением 500 кВ - 60 м, для 1150кВ - 110 м.
Предприятия по добыче нефти при выбросе сероводорода от 0,5 до 1 т/сут., а также с высоким содержанием летучих углеводородов относятся к первому классу и должны иметь СЗЗ не менее 1000 м.